
Lightweighting trends in battery tray aluminum profiles
Release Time:
2022-09-07
The lightweight development trend of battery tray aluminum profiles is clear and obvious. Aluminum is still a material with significant lightweighting effects. However, due to cost factors, the application of battery tray aluminum profiles varies across different vehicle models. Early Tesla models were aggressive in lightweighting applications. In the early Model S, aluminum accounted for a large proportion of the vehicle body and battery system structure. This was because the target consumer group for the Model S at that time was luxury customers. The proportion of aluminum in global automotive applications is increasing. The reason for using aluminum for lightweighting is that it meets and conforms to the new product's environmental protection, energy saving, and lightweight development trends. The use of low-cost high-strength steel plates is a reasonable market behavior. Tesla is not always a technological fanatic. Considering cost factors, adjusting the amount of aluminum used is also a reasonable technical behavior. In the Model 3 design, the design concept changed from the previous "radical" and "luxury," and the body structure adopted a steel-aluminum mixed metal material, reducing the proportion of aluminum used. Even the designers of the well-known Volkswagen MEB platform have indicated that they prefer low-cost thick steel plates, and that new energy vehicles are not simply...
Aluminum profile for battery tray The trend towards lightweight development is clear and obvious. Aluminum remains a material with significant lightweighting effects. However, due to cost factors, the use of aluminum profiles for battery trays varies across different vehicle models.
Early Tesla models were pioneers in lightweight applications. In the early Model S, aluminum accounted for a large proportion of the vehicle, from the body to the battery system structure. This was because the target consumer group for the Model S at that time was high-end customers.
The proportion of aluminum in global automotive applications is increasing. The use of aluminum for lightweighting properties is in line with the trend towards environmental protection, energy saving, and lightweighting of new products. The use of cost-effective high-strength steel plates is a reasonable market behavior.
Tesla is not always a technological fanatic. Considering cost factors, adjusting the amount of aluminum used is also a reasonable technical decision. In the Model 3 design, the design concept changed from the previous "radical" and "luxury", adopting a steel-aluminum mixed metal body structure, reducing the proportion of aluminum used.
Even the designers of the well-known Volkswagen MEB platform have indicated a preference for low-cost thick steel plates, stating that new energy vehicles are not simply "high-class fashion".
In reality, one material is unlikely to completely replace another. Any material, from a cost perspective or a performance perspective, has its own advantages and disadvantages, and they coexist and develop continuously. It can only be said that a material may better meet the needs of technological or market innovation in a certain aspect.
The main drivers for the use of aluminum in new energy vehicles are still lightweighting and energy-saving requirements. Currently, taking a 40 kWh battery system as an example, if a steel structure is used, the cost can be controlled within 1,000 yuan; if an aluminum alloy profile welded shell structure is used, the cost is between 3,000 and 5,000 yuan. The cost ratio of aluminum alloy profiles is still 3 to 5 times that of steel.
In the promotion and use of aluminum in new energy vehicles, cost is still a stumbling block. However, this does not hinder technological progress and development. Currently, what are the design differences caused by the differences in the properties of steel and aluminum?
Steel and aluminum materials have significant differences, Aluminum profile for battery tray Structural design needs to be more "tailored".
Steel and aluminum materials have significant differences in parameters such as compressive strength, fatigue resistance, elastic modulus, tensile strength, compressive strength, bending resistance, and bending strength. The use of alloy technology has indeed significantly improved certain aspects, such as compressive strength, compared to pure aluminum. However, the strengthening of a single property does not equate to a substantial property migration or complete transformation.
Related News
Copyright © 2022 Henan Junmei Aluminum Industry Co., Ltd.
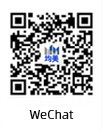
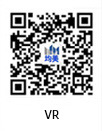
Tel:+86-371-56036666
Email:junmeily@126.com
Contact:+86-13838526418 Han
Address:No. 108, Minzu Road, Ludian Office, Dengfeng City, Henan Province