
Comparison of aluminum profile and steel structure design schemes for battery trays
Release Time:
2022-09-05
Especially in the field of vehicle engineering, the differences in characteristics under dynamic and static data loads are more obvious in steel structure design. We all know that in structural design, even if the parts have exactly the same function, an aluminum alloy profile structure cannot be equivalent to a steel structure design scheme. Let's illustrate this with a few examples. The design scheme of the battery tray aluminum profile bolted structure is passively compliant with the vehicle body structure and cannot meet the compressive strength requirements. For a long time, China's new energy vehicles have not been positively designed. The vehicle body structure or service platform is derived from gasoline vehicles. The vehicle body structure has not been modified or designed for much adaptability. In this case, the design scheme for the battery tray aluminum profile and the vehicle body fixing position and method can only follow suit. However, with the expansion and popularization of the new energy market, the operational safety of the battery system is increasingly valued, and this design scheme cannot meet the new design requirements. For early-stage manufactured new energy technologies, common failures such as bolt cracking, invalid IP, and invalid internal module structure leading to invalid electrical performance during customer use are all directly or indirectly caused by the unreasonable design of the battery tray aluminum profile bolted structure.
The difference in characteristics under dynamic and static data loads is particularly evident in the design of steel structures, especially in vehicle engineering.
We all know that in structural design, even if the parts have exactly the same function, an aluminum alloy profile structure cannot be equivalent to a steel structure design scheme. Let's illustrate this with a few examples.
Aluminum profile for battery tray The bolt structure design scheme is passively compliant with the vehicle body structure and cannot meet the compressive strength requirements.
For a long time, China's new energy vehicles have not been forward-designed. The vehicle body structure or service platform is derived from gasoline vehicles. The vehicle body structure has not been modified or designed for adaptability. In this case, the design scheme for the battery tray aluminum profile and its fixing position and method on the vehicle body can only follow suit.
However, with the increasing size and popularization of the new energy market, the operational safety of the battery system is becoming increasingly important, and this design scheme cannot meet the new design requirements.
For early-stage manufactured new energy technologies, common failures encountered by customers include cracked commodity bolts, invalid IP, and invalid internal structural module structure resulting in invalid electrical performance. Aluminum profile for battery tray The unreasonable design of the bolt structure is one of the direct or indirect main causes.
Rationalization of the customized support points of the tray bolts
The battery itself has a high relative density. As a load-bearing battery module, the battery tray or casing is always under heavy load. The fatigue performance of aluminum is only half that of steel; the elastic modulus of aluminum is only one-third that of steel.
If Aluminum profile for battery tray The bolt load exceeds the limit, or the difference in bearing capacity between different bolts is large and uneven. In response to the complex real-time road conditions of the vehicle, the dynamic performance is more extreme. Under high vibration and high stress conditions, aluminum materials are more prone to fatigue, resulting in cracking and deformation.
We all know that it is not surprising that cracks and other failures occur in the bolt area and inner frame column structure of the tray, or even that the module support points fall off.
Effective tray bolt support point design, the inner and outer frame structures are "perfectly integrated"
Ensuring that the battery module and the load-bearing tray are perfectly integrated is not an easy task. Withstanding the test of vibration tests is also a good way to verify the design conclusions.
During the intense testing, cracks in the welding of the inner frame and tray and cracks in the inner frame beam plate are often encountered. Basic analysis of the cause of cracking:
From the perspective of material properties, the stress at the failure point exceeds the stress that the material itself can bear.
From a technical perspective, the ablation caused by material welding changes or weakens the main parameter characteristics of the material.
From a structural perspective, whether the cracked beam plate is an integral part of the inner frame structure. An integral structure is more conducive to stress dispersion and uniform pressure, and consistent vibration frequency.
Related News
Copyright © 2022 Henan Junmei Aluminum Industry Co., Ltd.
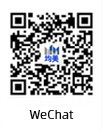
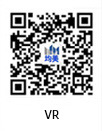
Tel:+86-371-56036666
Email:junmeily@126.com
Contact:+86-13838526418 Han
Address:No. 108, Minzu Road, Ludian Office, Dengfeng City, Henan Province